System serwo dla maszyny CNC
Wstęp
Tokarka CNC to precyzyjna i wydajna zautomatyzowana obrabiarka. Posiada szeroki zakres właściwości przetwórczych, obróbkę cylindrów liniowych, cylindrów skośnych, łuków kołowych i różnych gwintów. Ma różne funkcje kompensacyjne, takie jak interpolacja liniowa i interpolacja kołowa, i odegrał dobry efekt ekonomiczny w masowej produkcji skomplikowanych części. Tokarka CNC jest najczęściej używaną obrabiarką CNC w Chinach i ma największy zasięg, stanowiąc około 25% całkowitej liczby obrabiarek CNC.
Narodziny tokarek CNC mają epokowe znaczenie dla ludzkiej obróbki skrawaniem. Produkcja detali również przeniosła się na drogę dużej objętości, wysokiej precyzji i wysokiej stabilności. Dla kraju udział obrabiarek CNC we wszystkich urządzeniach do cięcia metalu jest ważnym parametrem pozwalającym zmierzyć poziom automatyzacji. Ma ogromne znaczenie dla rozwoju gospodarki narodowej i siły kraju.
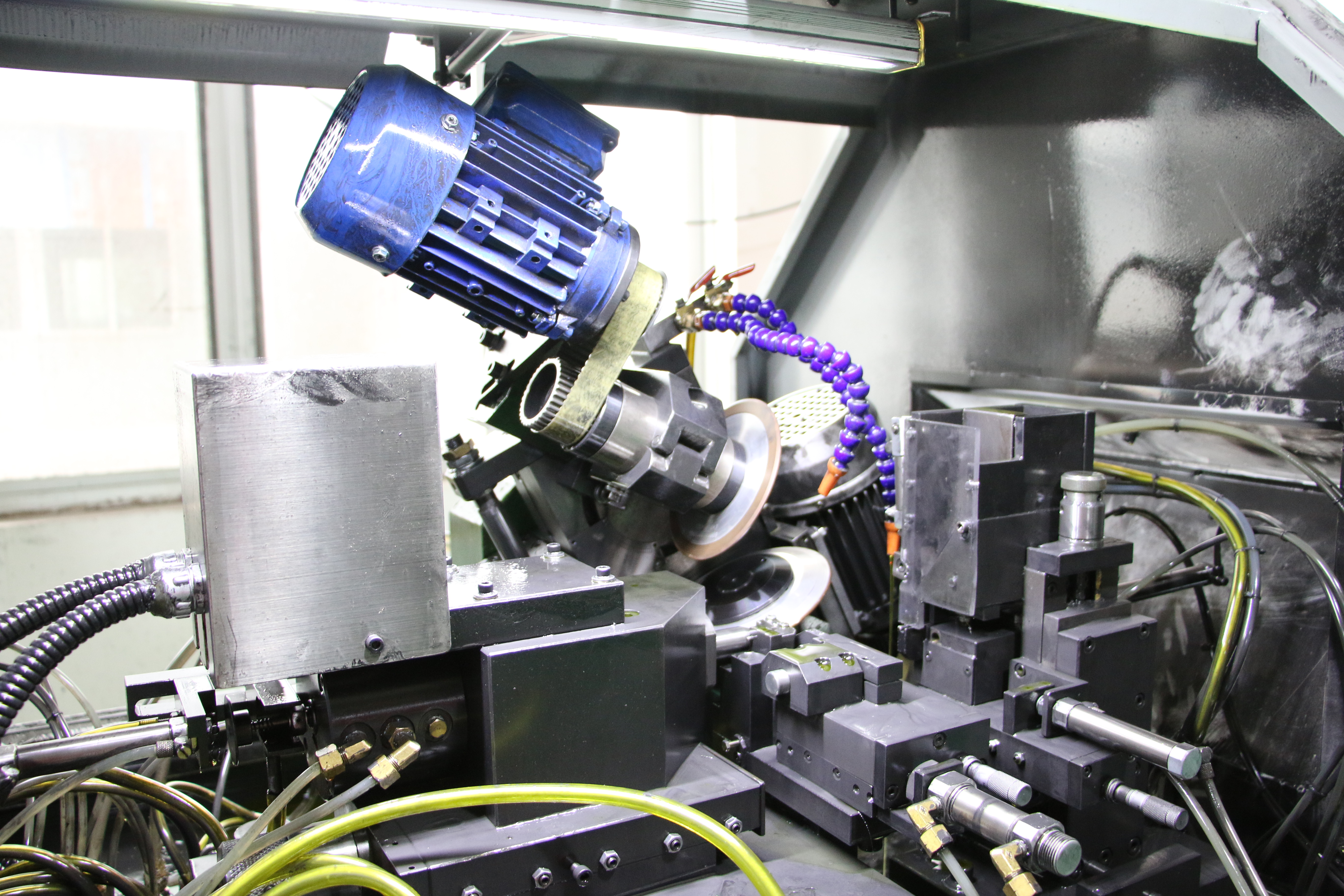
Tokarki CNC
Obrabiarka sterowana cyfrowo - Obrabiarka CNC, jej angielska nazwa to CNC MACHINE TOOLS. Jest to urządzenie elektromechaniczne, które podlega automatycznej obróbce za pomocą zaprogramowanego programu obróbczego. Istnieje wiele rodzajów obrabiarek CNC, w tym tokarki CNC, szlifierki CNC, wytaczarki CNC, strugarki CNC, frezarki CNC, tokarki pionowe CNC itp. Obejmuje również pionowe centrum tokarsko-frezarskie, poziome centrum frezarskie i wytaczarskie , suwnicowe centrum wytaczarsko-frezarskie, centrum tokarsko-frezarskie CNC, maszyna do cięcia wzdłużnego CNC i inne obrabiarki CNC do obróbki kompozytów. Ponadto w ostatnich latach szybko rozwinęły się nowe maszyny EDM, maszyny do cięcia laserowego, obrabiarki do cięcia wodą, obrabiarki do cięcia drutu, równoległe obrabiarki CNC i zautomatyzowane linie produkcyjne obrabiarek złożonych.
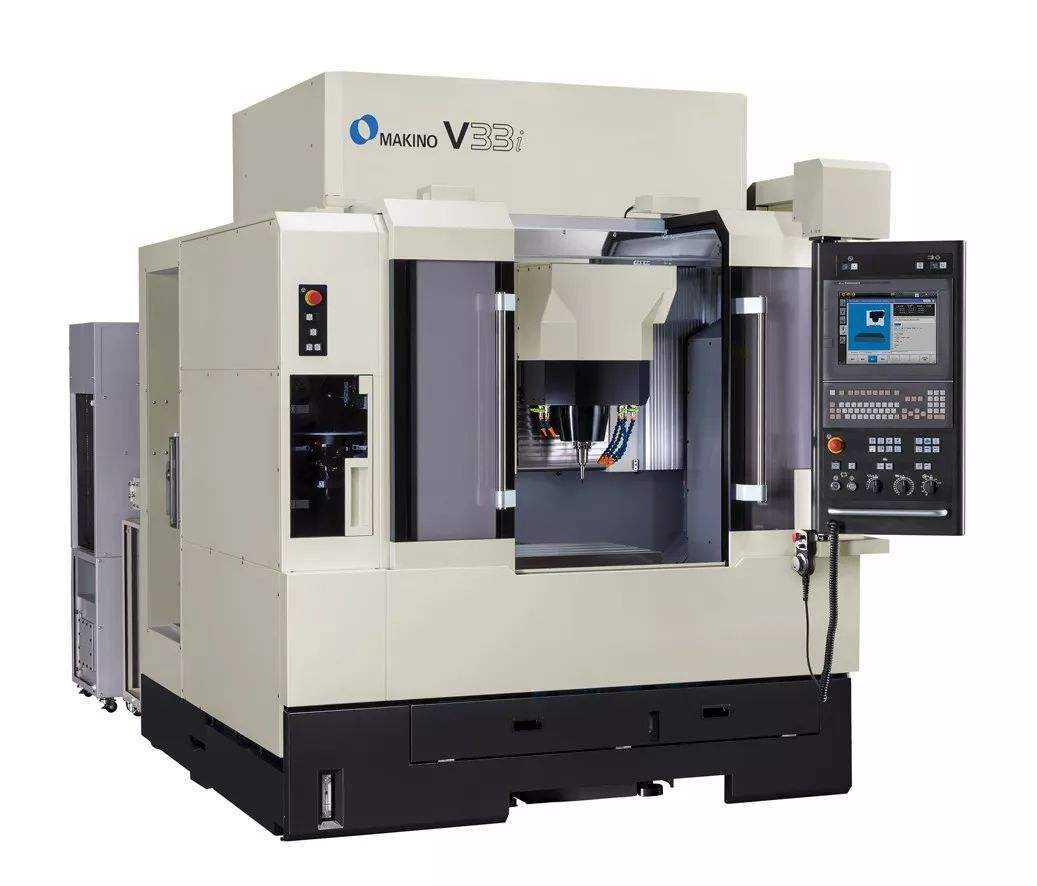
Obrabiarka CNC
Co to jest tokarka CNC?
Tokarka to obrabiarka, która głównie toczy obracający się przedmiot za pomocą narzędzia tokarskiego. Stosowana głównie do obróbki wałów, tarcz, tulei i innych detali z powierzchnią obrotową, jest najpowszechniej stosowanym typem maszyny w zakładach produkcji i napraw mechanicznych. Tokarka CNC, znana również jako tokarka CNC, jest skomputeryzowaną tokarką sterowaną cyfrowo, która jest precyzyjną i wydajną zautomatyzowaną obrabiarką. Posiada szeroki zakres właściwości przetwórczych, obróbkę cylindrów liniowych, cylindrów skośnych, łuków kołowych i różnych gwintów. Ma różne funkcje kompensacyjne, takie jak interpolacja liniowa i interpolacja kołowa, i odegrał dobry efekt ekonomiczny w masowej produkcji skomplikowanych części. Tokarka CNC jest najpowszechniej stosowaną obrabiarką CNC w Chinach o największym zasięgu, stanowiącym około 25% całkowitej liczby obrabiarek CNC. Obrabiarki CNC to produkty mechatroniczne integrujące mechanikę, elektrykę, hydraulikę, pneumatykę, mikroelektronikę i technologie informacyjne. Jest to maszyna robocza o wysokiej precyzji, wysokiej wydajności, wysokiej automatyzacji i dużej elastyczności mechanicznego sprzętu produkcyjnego.
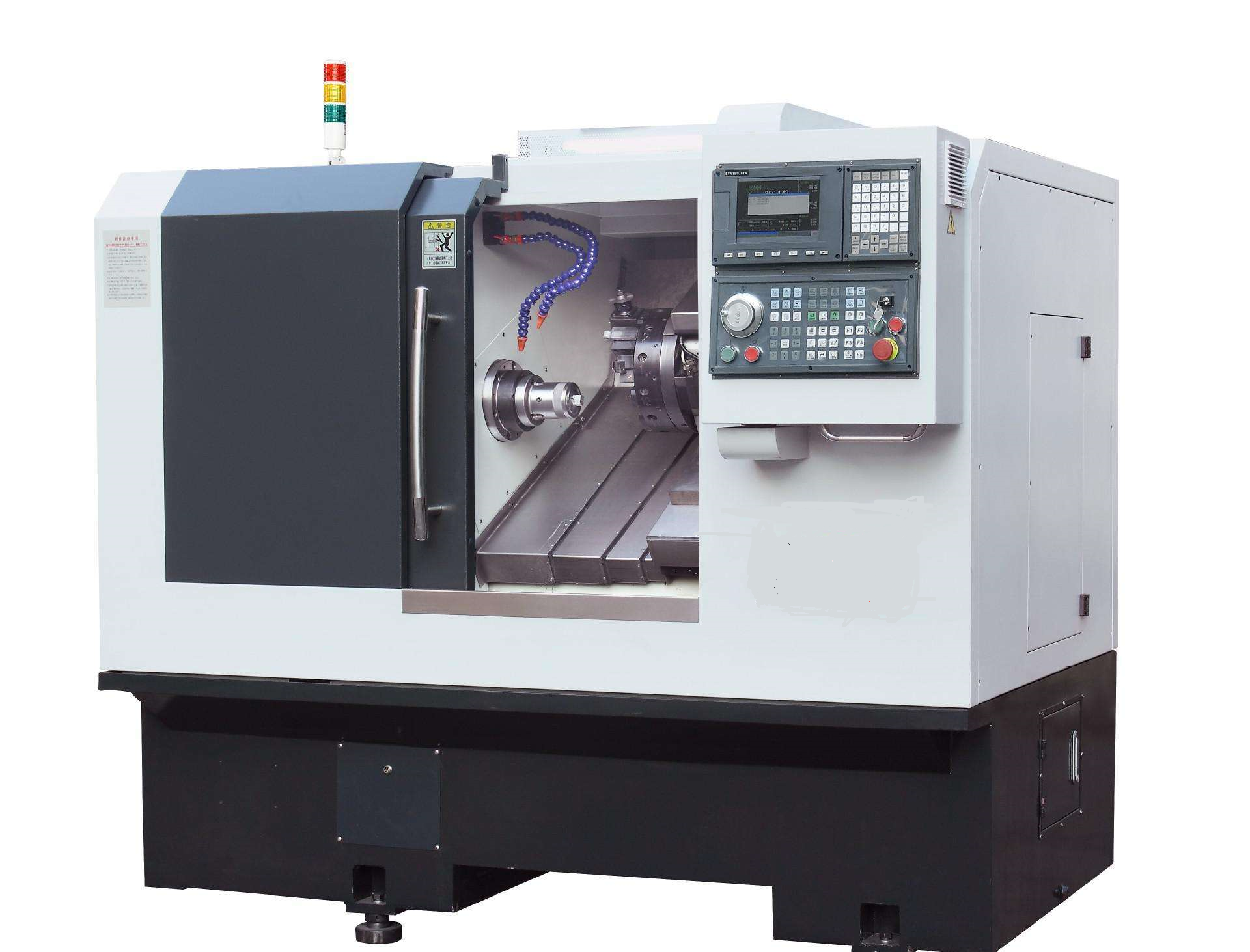
Obrabiarki CNC
Stan rozwoju tokarki
Jako maszyna główna wszystkich maszyn do obróbki metalu, tokarka stworzyła od 1797 roku nowoczesną tokarkę z uchwytem narzędziowym z napędem śrubowym. Odkąd brytyjski wynalazca mechaniki Mozli stworzył nowoczesną tokarkę z uchwytem narzędziowym z napędem śrubowym, nastąpił ogromny postęp rozwój przemysłu obróbki mechanicznej. Rozwój tokarek na świecie przeszedł od zwykłych tokarek do hydraulicznych półautomatów, zautomatyzowanych, do sterowania numerycznego, aż do dzisiejszego inteligentnego, sieciowego procesu rozwoju, w którym relacje między maszynami i ludźmi stają się coraz bardziej uproszczone, od polegając na biegłości w zapewnieniu jakości przedmiotu obrabianego, wprowadzając jedynie program NC, można uzyskać produkty wysokiej jakości i wysokiej wydajności, a tokarka staje się coraz bardziej humanizowana, w dostosowywaniu się do warunków pracy, wymagań procesu, specjalizacji, ochrona środowiska i inne aspekty wkroczyły do nowoczesnej hali. Kraje zachodnie, w tym Niemcy, Stany Zjednoczone i Japonia, opracowały wcześniejsze tokarki, zwłaszcza tokarki CNC, i zgromadziły bogate doświadczenie w rozwoju tokarek. Ich obrabiarki utrzymują wiodącą pozycję pod względem poziomu technicznego, zachowania precyzji, obróbki kompozytów z dużą prędkością i szerokiej gamy akcesoriów. Chociaż Chiny rozpoczęły działalność późno, przeżyły etapy wprowadzania technologii, trawienia i ponownej innowacji. Ma absolutną przewagę na rynku low-end, a wciąż brakuje mu high-endu, zwłaszcza wysokiej precyzji, dużej prędkości i dużej złożoności. Historia rozwoju tokarek zewnętrznych CNC w połączeniu z obecną dojrzałością technologii, rozwój tokarek CNC odzwierciedla następujące cechy:
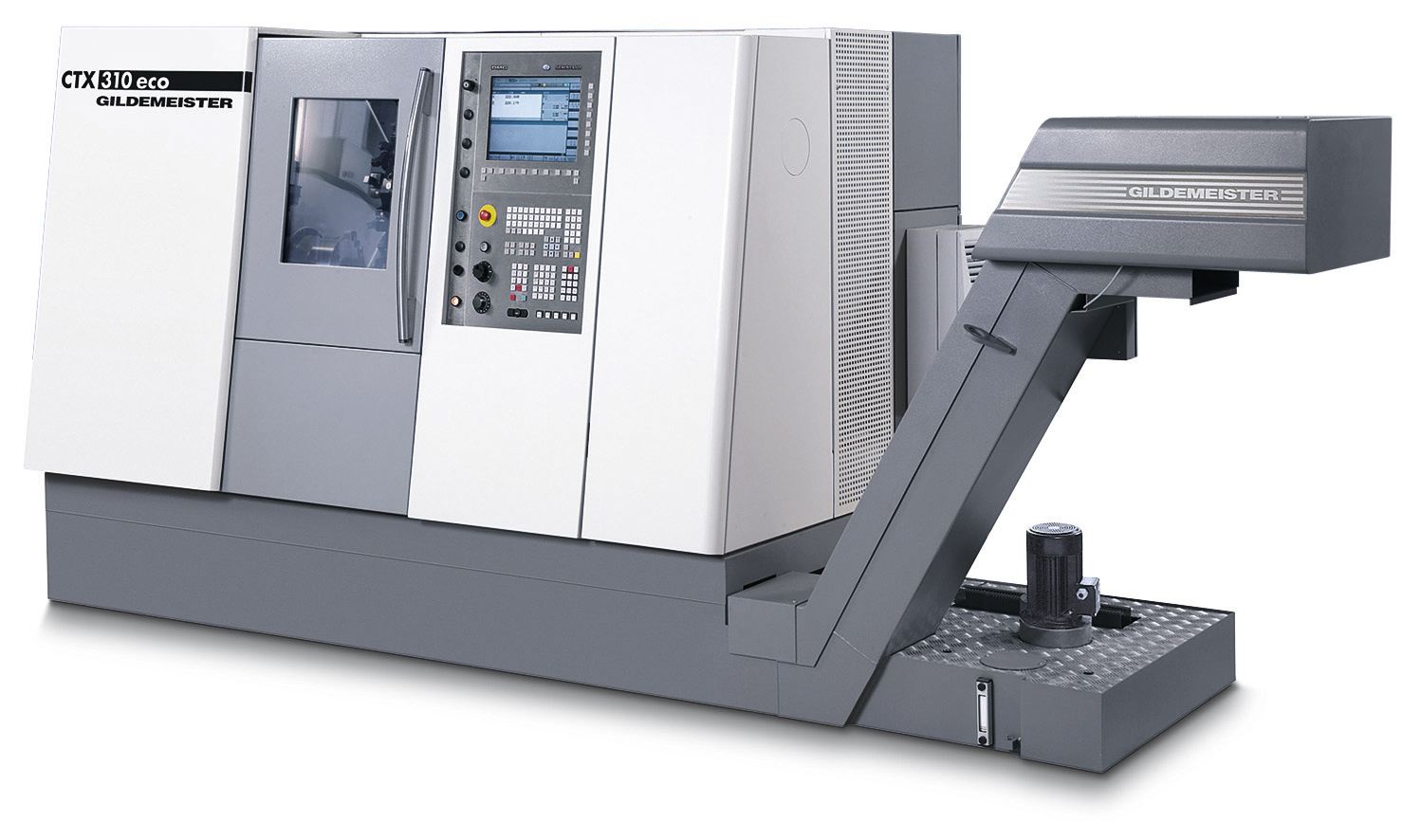
Tokarki CNC
(1) Szybkie, precyzyjne i złożone przetwarzanie stało się głównym nurtem. W zakresie obróbki ogólnej stosowane obecnie na rynku tokarki powszechne i ekonomiczne tokarki CNC są obrabiane na poziomie IT7, a ich prędkość wrzeciona jest niska, a prędkość posuwu szybkiego jest niska. Będzie ono stopniowo eliminowane w ciągu najbliższych 5-10 lat. Zastąpiona przez większe prędkości, wyższe prędkości wrzeciona i szybciej poruszające się obrabiarki liniowe, rewolucja w całej erze tokarek CNC została osiągnięta w Stanach Zjednoczonych, Niemczech, Japonii, Korei Południowej i na Tajwanie. Stopniowo wdrażane w krajach rozwijających się, takich jak Chiny i Indie. W wielu badaniach naukowych, przemyśle lotniczym i wojskowym, ze względu na bardziej rygorystyczne wymagania dotyczące precyzji obróbki, błędów kształtu i położenia oraz błędów konturu detali, zapotrzebowanie na obróbkę kompozytową obrabiarek jest oczywiste. Na przykład wirnik silnika lotniczego często wymaga jednorazowego montażu, a obróbka różnych skomplikowanych powierzchni, otworów i rowków jest wykonywana jednocześnie, aby zapewnić dokładność. Niezbędna jest zdolność obrabiarki do wykonywania obróbki kompozytowej, a precyzję przedmiotu obrabianego można zapewnić precyzją obrabiarki. Ten typ maszyn reprezentowany jest przez centrum obróbcze CNC serii DMG CTX.
(2) Funkcje wykrywania i kompensacji błędów online stopniowo zyskują na popularności. Dzięki innowacyjnemu rozwojowi technologii systemów CNC, technologii internetowej i technologii czujników mamy możliwość realizacji wykrywania i kompensacji detali online na tokarkach CNC. W rzeczywistym procesie obróbki, na skutek działania sił i odkształceń termicznych elementów maszyny, dokładność obróbki ulega zmniejszeniu. Technologia wykrywania i kompensacji online dobrze rozwiąże ten problem, a te zaawansowane technologie zostały spopularyzowane w urządzeniach ogólnego przeznaczenia. Używana jest głównie amerykańska seria Haas.
(3) Inteligentne, połączone w sieć i elastyczne. Rozwój Internetu daje nieograniczone możliwości rozwoju obrabiarek CNC. Wraz z popularnością i dojrzałością sieci, bohaterami czasów staną się obrabiarki wyposażone w interfejsy internetowe. Dzięki realizacji IOT i interoperacyjności za pośrednictwem sieci przyszłe obrabiarki będą mogły komunikować się ze sobą, monitorować w czasie rzeczywistym, przekazywać informacje zwrotne w czasie rzeczywistym, analizować i wykorzystywać stan pozycji maszyny, stan przedmiotu obrabianego i inne dane, znacznie poprawiając wydajność produkcji . Opieranie się na danych może również umożliwić zdalną produkcję sieciową i produkcję zindywidualizowaną w celu stworzenia prawdziwego Internetu przemysłowego. Tę serię obrabiarek reprezentują obrabiarki serii i5 firmy Shenyang Machine Tool.
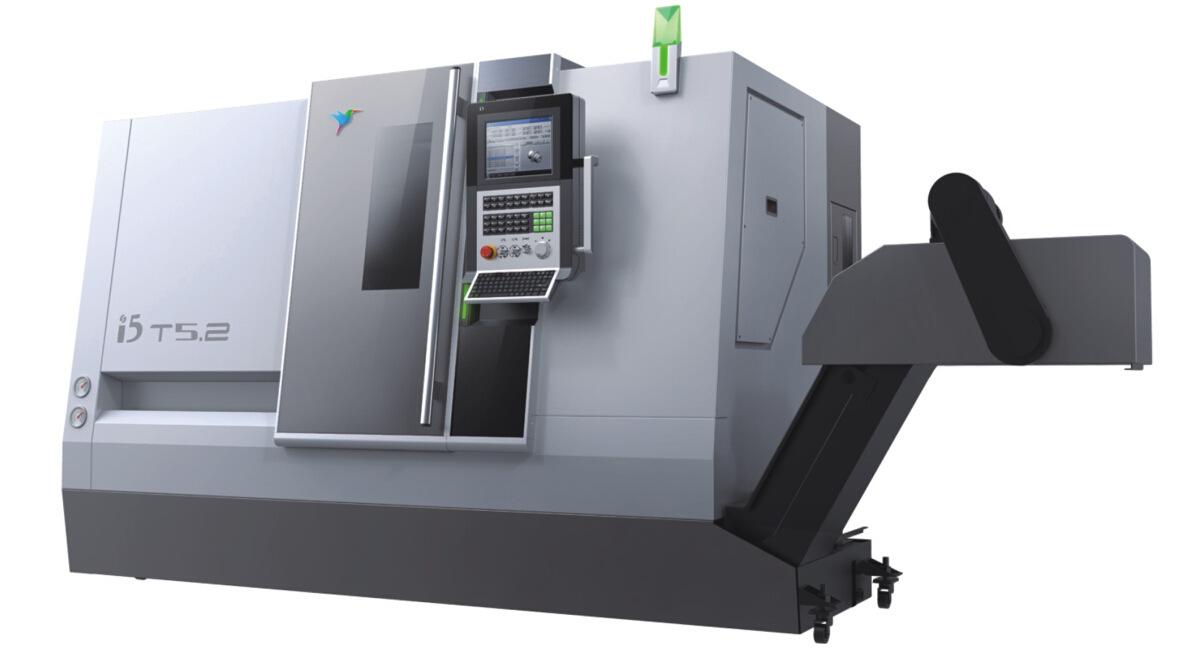
Obrabiarka CNC
Części silników tokarek CNC
1. Uchwyt narzędziowy
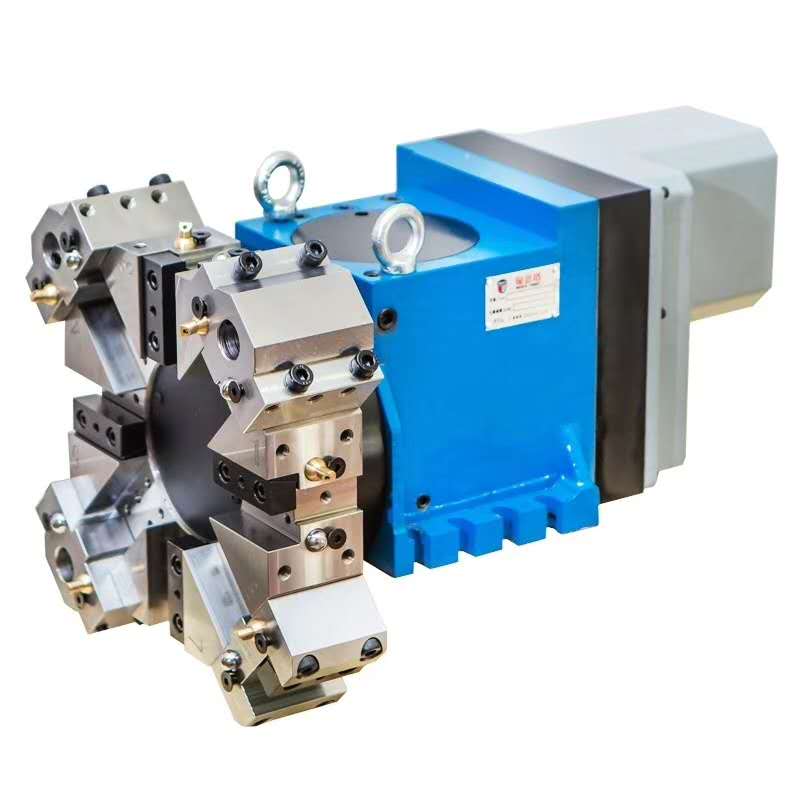
Uchwyt na narzędzia
Jako kluczowa funkcja tokarki CNC, uchwyt elektronarzędzia pełni bardzo ważną funkcję, służącą głównie do realizacji funkcji mocowania narzędzia, magazynowania narzędzia i automatycznej wymiany narzędzia. Na rynku oprawki narzędziowe CNC dzieli się zazwyczaj na niskie, średnie i wysokie. Klasyfikacja zależy głównie od okazji użycia. Niskiej jakości uchwyt narzędziowy zazwyczaj wykorzystuje jako energię wyłącznie energię elektryczną, co nazywa się po prostu elektrycznym uchwytem narzędziowym. Ponieważ jako źródło siły momentu obrotowego uchwytu narzędziowego wykorzystywany jest wyłącznie moment obrotowy silnika, nie może on pełnić zbyt wielu funkcji, ale prostota konstrukcji również to powoduje. Elektryczny uchwyt narzędziowy z niższej półki ma dużą nośność , a jego niska prostota decyduje, że nie można go zastosować w maszynach o wysokiej precyzji i wymaganiach wielu, a można go stosować tylko na ekonomicznych i prostych obrabiarkach. Uchwyt narzędziowy średniej klasy ma pewne ulepszenia i istnieje wiele typów, głównie hydrauliczny uchwyt narzędziowy, uchwyt narzędziowy serwo i elektryczny uchwyt narzędziowy podwójnego wyboru. Zgodnie z nazwą uchwytu narzędziowego, hydrauliczny uchwyt narzędziowy napędzany jest głównie silnikiem hydraulicznym lub cylindrem hydraulicznym. Serwo wykorzystuje silnik serwo jako źródło zasilania. Ma wyższe wymagania w zakresie kontroli i precyzji, jest szybszy i powtarza dokładniejsze pozycjonowanie. Ten uchwyt narzędziowy średniej klasy jest szeroko stosowany w zwykłych obrabiarkach ze względu na jego zastosowanie i cenę. W porównaniu z oprawką narzędziową średniej klasy, oprawka narzędziowa CNC wysokiej jakości charakteryzuje się lepszym poziomem wydajności, głównie pod względem precyzyjnego utrzymania i obróbki o wysokiej precyzji. Wysoka automatyzacja to także kierunek rozwoju wysokiej jakości oprawek narzędziowych. Do zaawansowanych obrabiarek CNC o wysokich wymaganiach dotyczących precyzji.
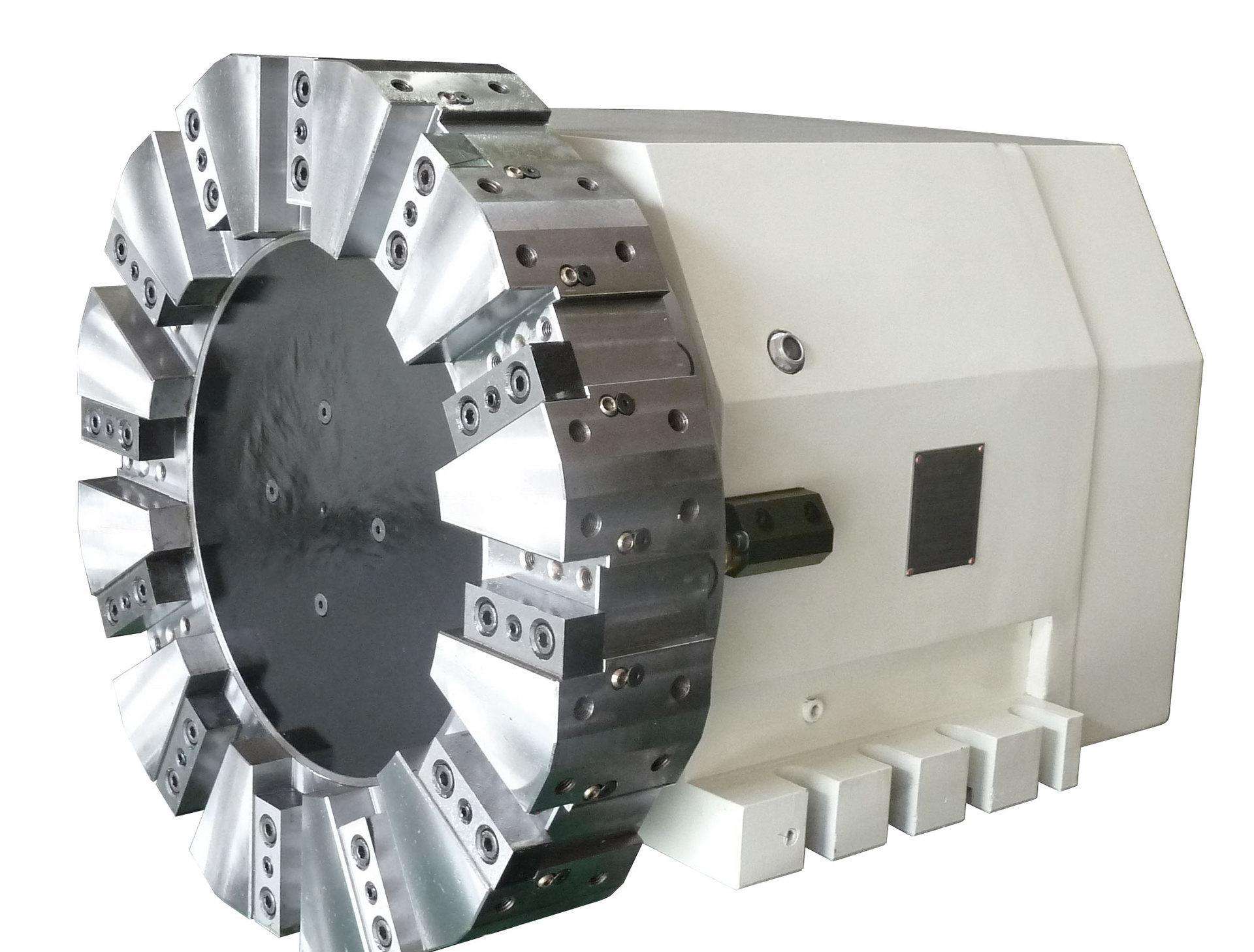
Hydrauliczny uchwyt narzędziowy
Historia rozwoju uchwytów do elektronarzędzi sięga lat 80-tych. Dzięki ponad 30-letniemu rozwojowi jako kluczowemu elementowi obrabiarek CNC coraz większą uwagę zwraca się na jego znaczenie. Wykorzystuje się niezawodność i wydajność uchwytu elektronarzędzia. Stabilność góry odgrywa ważną rolę w poziomie niezawodności całej maszyny. Dzisiejsze oprawki narzędziowe na świecie są skupione w Niemczech, Włoszech, Wielkiej Brytanii i innych bardziej rozwiniętych krajach Europy. Ze względu na długą historię rozwoju, akumulacja technologii jest stosunkowo silna, zespół badawczy jest również na najwyższym poziomie, a projektowane i produkowane przez niego oprawki narzędziowe są niezawodne. Wyższa wydajność. Do najsłynniejszych na świecie oprawek narzędziowych należą Schott w Niemczech, Balafa we Włoszech i Dupumadik, którzy zajmują się rynkiem średniej i wyższej półki.
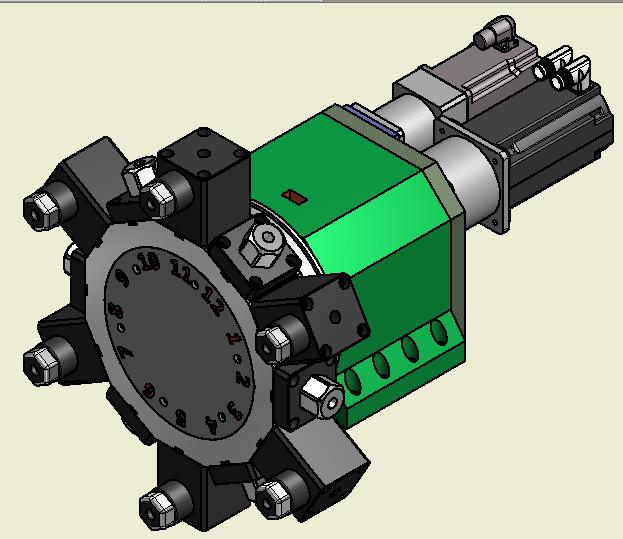
Uchwyt noża elektrycznego
Tabela dystrybucyjna różnych producentów oprawek narzędziowych
2. Serwo podawania
Układ serwonapędu składa się z trójpierścieniowej struktury obejmującej kontrolę położenia, kontrolę prędkości i kontrolę prądu.
1) Pętla prądowa
Pętla prądowa jest najbardziej wewnętrzną pętlą systemu. Jest to dolne łącze próbkowania danych całego układu serwo. Im krótszy okres próbkowania dyskretnej pętli prądowej, tym większa może być sztywność serwa i tym lepsza będzie wydajność sterowania serwem. Pętla prądowa jest pętlą najbardziej wewnętrzną, zatem pętla prądowa jest podstawą sterowania i najbardziej bezpośrednim wykonawcą całego sterowania. Ogólnie rzecz biorąc, ostatecznym celem regulacji serwomechanizmu jest zapewnienie, że niezależnie od tego, jak duża lub mała jest prędkość obróbki, konieczne jest zapewnienie możliwie największej stabilności prądu (składowa harmoniczna prądu na wyjściu pętli prądowej jest mała ) i nie wahaj się zbytnio. Obecna szybkość reakcji jest duża. Tylko stabilność prądu może zagwarantować stabilność momentu obrotowego i ostatecznie można zapewnić końcowy efekt obróbki. Ponadto, ze względu na szybki cykl przetwarzania, pętla prądowa umożliwia również szczegółowe wykrywanie anomalii sterowania. Pętla prądowa jako pętla najbardziej wewnętrzna musi spełniać dłuższy okres odpowiedzi niż pętla prędkości i pętla położenia, aby możliwe było dokładne sterowanie w czasie rzeczywistym ze względu na zmianę prędkości obrotowej. Częstotliwość prądu przemiennego może nadążać za przetwarzaniem poleceń wysyłanych przez pętlę prędkości i reagować na czas.
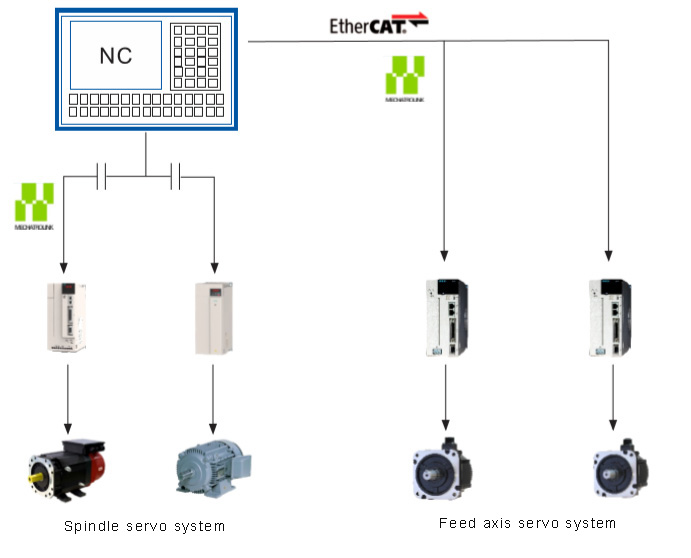
Rozwiązanie tokarki skośnej
2)Pętla prędkości
Pętla prędkości zapewnia zgodność prędkości silnika z wartością zadaną, eliminując wpływ zakłóceń momentu obciążenia i innych czynników na prędkość silnika. Zadana prędkość jest porównywana z rzeczywistą prędkością silnika w ramach sprzężenia zwrotnego. Różnica jest generowana bezpośrednio przez regulator prędkości w celu wygenerowania prądu sterującego osi q w celu sterowania przyspieszaniem, zwalnianiem lub równomierną prędkością silnika, tak aby rzeczywista prędkość silnika była zgodna z wartością zadaną.
Pętla prędkości to pośrednie połączenie pomiędzy pętlą prądową a pętlą położenia. Rozsądne zwiększenie pętli prędkości jest podstawą całego uruchomienia serwa. Pętla prędkości wykorzystuje całą pętlę prądową jako obiekt kontrolowany. Moment obrotowy jest iloczynem prędkości i bezwładności. Aby zapewnić stabilność momentu obrotowego, podstawowe znaczenie mają prędkość i rozsądny stosunek bezwładności obciążenia. Dlatego rolą pętli prędkości jest zapewnienie stabilności prędkości. Stosunek prędkości do bezwładności obciążenia bezpośrednio wpływa na stabilność pętli prądowej. Jednym z najważniejszych parametrów regulacji serwa jest wzmocnienie pętli prędkości (Kv).
Wzmocnienie pętli prędkości to różnica powiększenia danej prędkości w porównaniu z prędkością sprzężenia zwrotnego. Oczywiście im większa wielokrotność, tym wyższa rozdzielczość zmiany prędkości. Im wyższa rozdzielczość, tym silniejsza zdolność rozróżniania i odwracania wahań prędkości (ponieważ istotą ujemnego sprzężenia zwrotnego jest ciągłe korygowanie różnicy aż do zera). Ta zdolność do odwracania prędkości jest bardzo krytyczna, co oznacza, że anty- zdolność zakłócania tego systemu do obciążenia zewnętrznego, im większy przyrost prędkości, tym silniejsza zdolność przeciwzakłóceniowa systemu na zewnątrz, tym silniejsza zdolność do tłumienia wahań prędkości, tym lepsza jest płynność (bez wibracji)) . Dlatego im większe wzmocnienie pętli prędkości, które reprezentuje możliwość precyzyjnego sterowania prędkością, oznacza precyzyjną siłę momentu obrotowego, która reprezentuje najlepszą charakterystykę wygładzania powierzchni. Razem z pętlą położenia reprezentuje najlepszą responsywność maszyny.
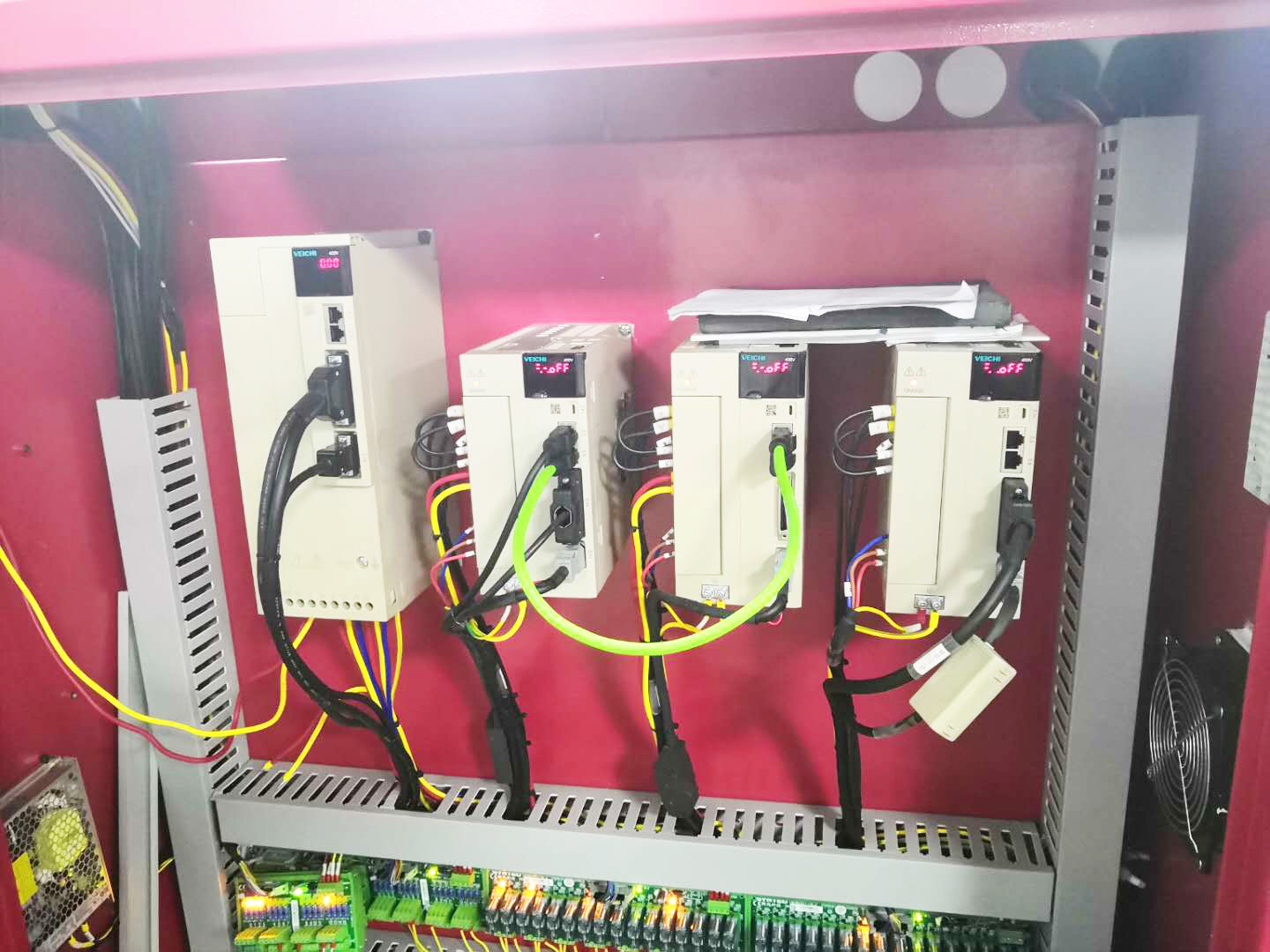
Serwonapęd VEICHI
3) Pętla pozycyjna
Podstawowym zadaniem pętli położenia jest umożliwienie siłownikowi dokładnego śledzenia poleceń położenia, co może generować polecenia prędkości dla silnika oraz dokładne pozycjonowanie i śledzenie silnika. Ustawiając pozycję docelową w porównaniu z rzeczywistą pozycją, w której silnik jest dokładnie ustawiony, pozycja silnika jest wykorzystywana do generowania polecenia prędkości silnika. Gdy podana kwota zmienia się losowo, system może dokładnie i dokładnie śledzić i odtworzyć podaną kwotę. Jak widać na schemacie blokowym układu serwonapędu, pętla pozycyjna jest najbardziej zewnętrznym pierścieniem wewnątrz trzech pierścieni i stanowi końcowy obiekt regulacji. Kontroluje wszystkie obiekty, w tym pętle prądowe i pętle prędkości.
Ogólnie rzecz biorąc, najpierw określana jest pętla prądowa i pętla prędkości, a na końcu określana jest pętla położenia. Dlatego po poleceniu położenia po interpolacji pętla położenia jest najważniejszym ostatecznym wyznacznikiem zapewniającym, że wynik obróbki spełnia wymagania. Aby ocenić wydajność obróbki obrabiarki, głównie pod względem wykończenia powierzchni i dokładności konturu obrabianych części, przy czym dokładność konturu jest określana z punktu widzenia systemu przez pętlę położenia. Po zapewnieniu sygnału wejściowego pętli położenia różnica jest wzmacniana za pomocą położenia sprzężenia zwrotnego zwróconego przez sprzężenie zwrotne i uzyskiwany jest błąd położenia. Oczywiście, podobnie jak wzmocnienie pętli prędkości, wzmocnienie pętli położenia opisuje zdolność dokładnego rozpoznawania zmian położenia. Jego rolą jest opisanie dokładności statycznej i wydajności dynamicznego śledzenia systemu. Im większe ustawienie KP korzyści dla pętli położenia, tym wyższa zdolność rozróżniania i zdolność skręcania zmiany położenia, histereza mechaniczna zostanie znacznie poprawiona, a wydajność dynamiczna będzie silniejsza. Dzięki wysokiej reakcji pętli prędkości ostatecznie poprawia się dokładność pozycjonowania.
Rozwój systemu serwo przeszedł kilka etapów
We wczesnych latach sześćdziesiątych XX wieku w obrabiarkach sterowanych numerycznie zastosowano hydrauliczny układ serwo. W porównaniu z ówczesnym konwencjonalnym silnikiem prądu stałego, układ cieczowy i serwo charakteryzowały się krótkim czasem reakcji, a serwomechanizm wytwarzający ten sam moment obrotowy miał niewielki kształt zewnętrzny. Jednakże hydrauliczny układ serwo ma wady polegające na dużym wytwarzaniu ciepła, niskiej wydajności, zanieczyszczeniu środowiska i niewygodnej konserwacji.
W połowie lat sześćdziesiątych XX wieku w obrabiarkach CNC powszechnie stosowano układ z otwartą pętlą składający się z serwosilnika krokowego o małej mocy i hydraulicznego wzmacniacza momentu obrotowego. Najbardziej reprezentatywnym z nich jest elektrohydrauliczny układ serwo silnika impulsowego japońskiej firmy. Jednak ze względu na złożoność struktury systemu i słabą niezawodność.
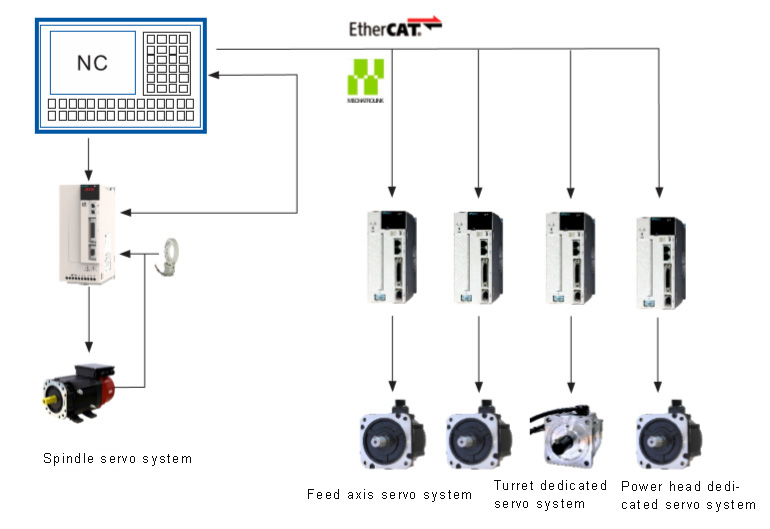
Program tokarsko-frezarski CNC
Pod koniec lat 60. XX wieku w obrabiarkach CNC szeroko stosowano silniki prądu stałego o małej bezwładności. Silnik prądu stałego o małej bezwładności sprawia, że konstrukcja silnika jest bardziej skomplikowana ze względu na dodanie przekładni pośredniej, która jest podatna na zużycie, zwiększa luz przekładni i wpływa na dokładność przekładni.
W latach 70. amerykańska firma GETTYS jako pierwsza opracowała silnik prądu stałego o dużej bezwładności, zwany zwykle silnikiem prądu stałego o dużej prędkości. Ma szeroki zakres prędkości i można go podłączyć bezpośrednio do śruby pociągowej. Znacząco upraszcza to dopasowanie do bezwładności ruchomych części podajnika maszyny. Od lat 70. silniki prądu stałego o dużej bezwładności są szeroko stosowane w różnego typu obrabiarkach CNC i osiągają dobre wyniki.
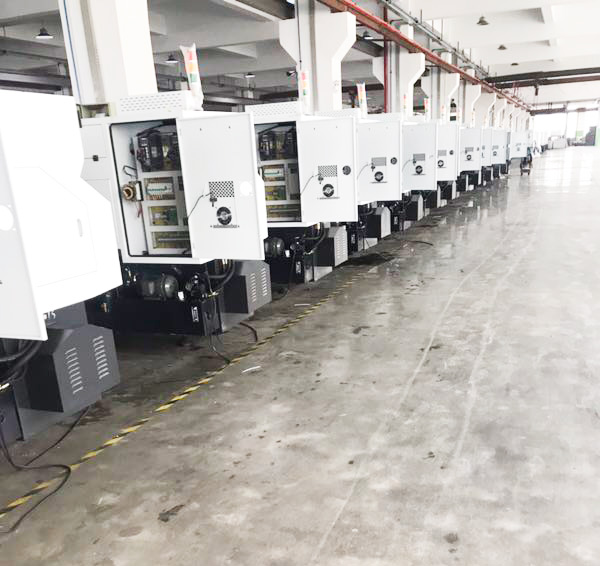
Obrabiarki CNC
Od lat 80. XX wieku, wraz z rozwojem wielkogabarytowych układów scalonych, energoelektroniki, technologii sterowania komputerowego, zwłaszcza komputera, w celu dokonania istotnego przełomu w technologii sterowania wektorowego pola magnetycznego silników prądu przemiennego, ludzie próbują zastąpić silniki prądu stałego silnikami prądu przemiennego na długi czas. Zrealizowano koncepcję zastosowania silnika w regulacji prędkości i sterowaniu serwomechanizmem. System serwo AC zachowuje prawie wszystkie zalety systemu prądu stałego i ma doskonałe parametry techniczne, takie jak szeroki zakres regulacji prędkości, dokładność przy dużych prędkościach i dobre charakterystyki reakcji dynamicznej, a także dziedziczy wiele doskonałych osiągów właściwych dla samego silnika prądu przemiennego.
W ostatnich latach na całym świecie pojawiło się wiele urządzeń przetwórczych wykorzystujących systemy serwo z zasilaniem silnika liniowego. Na Europejskich Targach Obrabiarek w Hanowerze w 1993 r. Niemcy zaprezentowały pierwsze na świecie liniowe centrum obróbcze z silnikiem liniowym, które zapoczątkowało system serwo z silnikiem liniowym. Serwo liniowe to idealny tryb jazdy dla szybkich i precyzyjnych obrabiarek CNC. Będzie to charakterystyczna cecha nowej generacji obrabiarek CNC, zarówno za granicą, jak i w krajowych badaniach i eksploracjach.
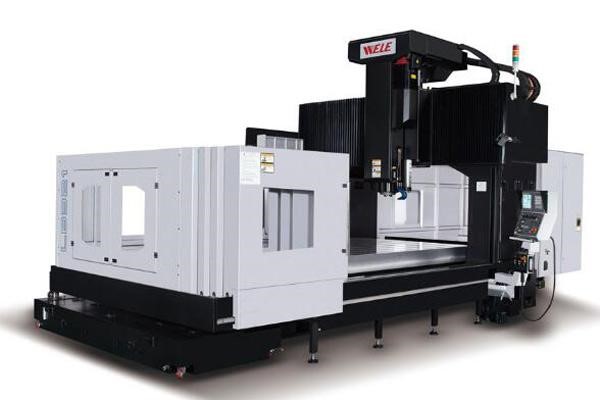
Obrabiarki CNC
Wymagania dotyczące systemów zasilania serwo
System serwo to automatyczny system sterowania, którego kontrolowaną wielkością są parametry mechaniczne (pozycja, prędkość, przyspieszenie). Jego podstawowym wymaganiem jest to, aby wyjście systemu mogło szybko i dokładnie reagować na zmiany na wejściu poleceń. Podstawowe wymagania dla układu serwo to:
1) Dobra stabilność oznacza, że system może osiągnąć nowy lub powrócić do pierwotnego stanu równowagi po krótkim procesie regulacji pod wpływem danego sygnału wejściowego lub zakłócenia zewnętrznego.
2) Dokładność serwomechanizmu to dokładność dzięki któremu wyjście może podążać za wejściem. W przypadku precyzyjnie obrobionej obrabiarki CNC wymagana dokładność pozycjonowania lub dokładność obróbki konturu są zwykle rozdzielane.
3) Dobra reakcja jest jednym ze wskaźników jakości dynamicznej układu serwo, czyli reakcji śledzenia sygnał sterujący musi być szybki, a czas procesu przejścia musi być krótki, zwykle nie może przekraczać 200 milisekund, a nawet mniej niż kilkadziesiąt milisekund; Z drugiej strony granica procesu przejścia musi być stroma, co oznacza, że tempo wzrostu jest duże.
4) Czułość: wrażliwość systemu na zmiany parametrów jest niewielka, tj. Zmiany parametrów mogą w dużym stopniu wpływać na system. Odporność: system powinien charakteryzować się dobrą odpornością na zakłócenia zewnętrzne i hałas o wysokiej częstotliwości.
5) Wymagania dotyczące mechanicznego układu przeniesienia napędu; w celu zapewnienia dokładności przekładni i stabilności pracy układu posuwu maszyny CNC, przy projektowaniu mechanicznego urządzenia przekładniowego proponuje się następujące wymagania:
(1) Dokładność przekładni i dokładność pozycjonowania: Dokładność przekładni i dokładność pozycjonowania urządzenia do transmisji posuwu maszyny CNC odgrywają kluczową rolę w dokładności obróbki części. Niezależnie od położenia punktu, systemu sterowania liniowego lub systemu sterowania konturem, dokładność transmisji i dokładność pozycjonowania to główne wskaźniki charakteryzujące wydajność obrabiarek CNC.
(2) Szybkość reakcji powinna być duża: stół warsztatowy powinien być w stanie z czułością i dokładnością śledzić polecenia w określonym zakresie prędkości oraz wykonywać ruch jednoetapowy lub ciągły bez strat lub zjawiska wieloetapowości podczas pracy.
(3) Transmisja bez przerwy: Luz przekładni układ podawania ogólnie odnosi się do luzu wstecznego, czyli błędu odwrotnej martwej strefy, który występuje w parach przekładni całego łańcucha transmisyjnego, bezpośrednio wpływając na dokładność obróbki obrabiarki CNC; dlatego należy wyeliminować luz napędu i zmniejszyć błąd wstecznej martwej strefy.
(4) Dobra stabilność i długa żywotność: stabilność jest najbardziej podstawowym warunkiem prawidłowego działania układu zasilania serwa, szczególnie w przypadku posuw o niskiej prędkości bez pełzania i może dostosować się do zmian przyłożonego obciążenia bez rezonansu. Żywotność tak zwanego układu podawania odnosi się głównie do czasu, przez jaki utrzymywana jest dokładność przekładni i dokładności pozycjonowania obrabiarki CNC, a także zdolność każdego elementu przekładni do utrzymania oryginalnej precyzji produkcyjnej.
(5 ) Łatwy w użyciu i konserwacji: konstrukcja systemu podawania powinna być łatwa w utrzymaniu i konserwacji, minimalizując ilość prac konserwacyjnych w celu poprawy wykorzystania maszyny.
System serwo wrzeciona
Cechy i wymagania układu napędowego wrzeciona tokarki CNC:
Funkcją układu sterowania wrzecionem jest napędzanie wrzeciona zgodnie z wymaganiami programu. W trybie obróbki tokarki CNC wrzeciono napędza głównie przedmiot obrabiany, aby się obracał i współpracuje z wałem napędowym serwa posuwu, aby zakończyć ruch skrawania. Dokładność i prędkość regulacji położenia wrzeciona tokarki CNC nie jest tak wysoka, jak w przypadku układu serwo. Dlatego w siłownikach zastosowano zwykły silnik asynchroniczny prądu przemiennego. Drogie serwosilniki prądu przemiennego z magnesami trwałymi są rzadko używane. Generalnie stosuje się falownik + silnik asynchroniczny prądu przemiennego. „Metoda sterowania wektorowego i wykrywania prędkości enkodera.” Dzięki ciągłemu unowocześnianiu branży „serwonapęd wrzeciona + serwosilnik wrzeciona + zewnętrzny enkoder”; jest coraz szerzej stosowany w frezarce CNC i maszynie mieszającej ze skośnym korpusem, która może spełniać wymagania ogólnej obróbki części precyzyjnych i toczenia gwintów oraz regulować. Jest to wygodne i wygodne, a koszt budowy jest stosunkowo niski. Jest szeroko stosowany.
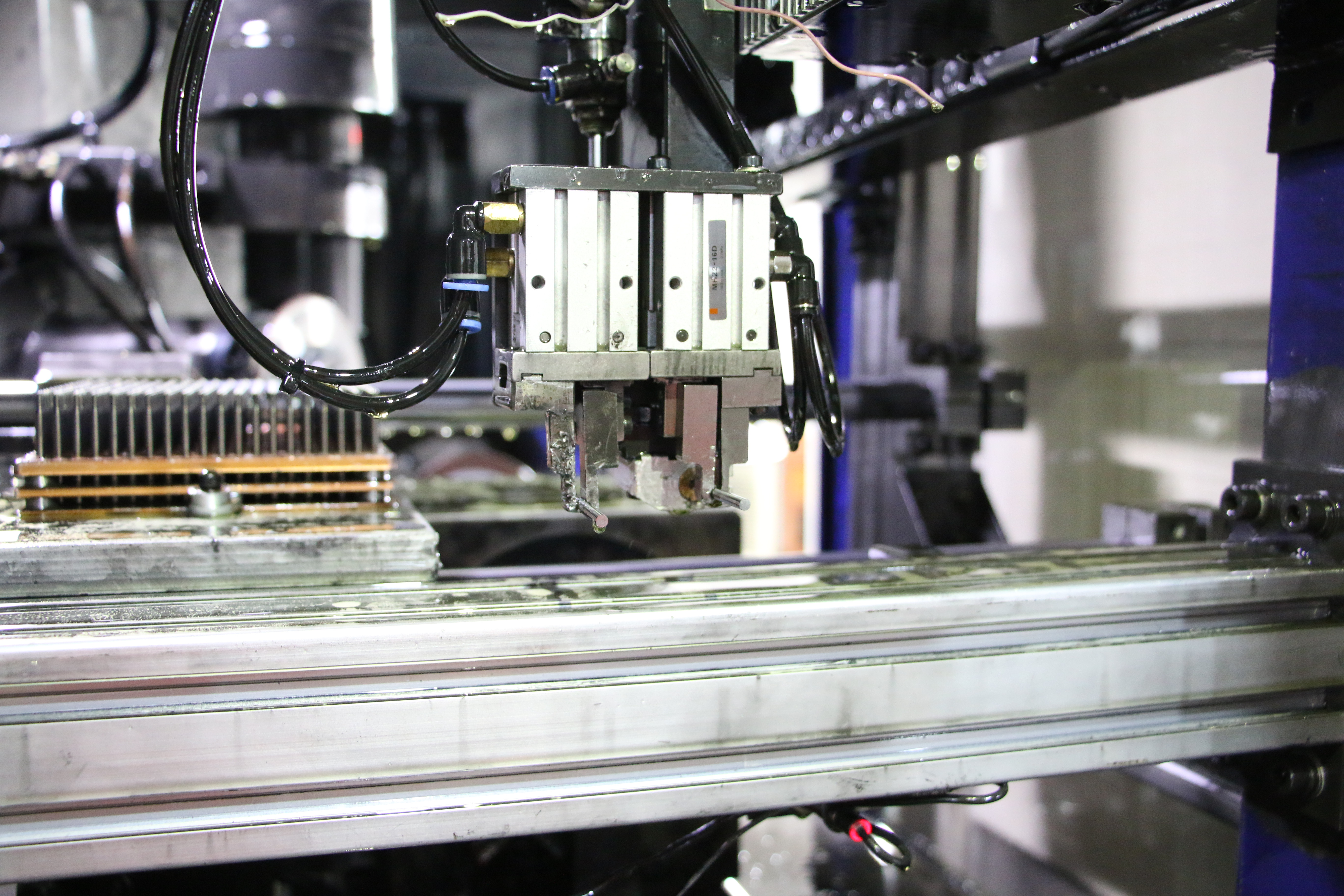
Układ napędowy wrzeciona tokarki CNC
Ruch wrzeciona tokarki CNC ma przenosić główną siłę skrawania, a pobierana moc stanowi około 60% całkowitej mocy maszyny. Dlatego układ napędowy musi mieć wystarczającą moc, sztywność i wystarczający moment obrotowy, aby utrzymać wystarczający moment obrotowy przy niskich prędkościach. Różne wymagania dotyczące prędkości wrzeciona w różnych procesach obróbki, takich jak toczenie gwintów, obróbka zgrubna i wykańczająca, wymagają szerokiego zakresu prędkości wrzeciona.
System serwo wrzeciona działa podobnie jak serwonapęd posuwu. Ma trzy pierścienie, ale wymagania dotyczące dokładności i reakcji nie są tak wysokie, jak wymagania serwa podającego. Generalnie serwomotor wrzeciona jest wyposażony w inkrementalne enkodery fotoelektryczne 2500. Producent dostosowuje się do transformatora obrotowego jako elementu sprzężenia zwrotnego w odpowiedzi na stosunkowo duże pole drgań.
Układ napędowy wrzeciona tokarki CNC
Istnieją 3 sposoby mechanicznego napędzania wrzeciona tokarki CNC
(1) Segmentowa, bezstopniowa zmiana prędkości. Silnik wrzeciona napędza wrzeciono w celu obracania się poprzez przekładnię skończoną. Ten tryb transmisji jest odpowiedni dla dużych obrabiarek CNC, zwłaszcza do wydajnego cięcia.
(2) Zmiana napędu pasowego. Silnik wrzeciona napędza obrót wrzeciona poprzez tryb przekładni z paskiem synchronicznym. Ten tryb transmisji jest odpowiedni dla małych i średnich obrabiarek CNC, szczególnie w sytuacjach, w których występują wysokie wymagania dotyczące odporności na wibracje;
(3) Silnik napędzany jest bezpośrednio. Silnik wrzeciona bezpośrednio napędza obrót wrzeciona poprzez sprzęgło lub bezpośrednio wykorzystuje wrzeciono elektryczne. Ta metoda transmisji jest odpowiednia dla małych obrabiarek CNC, zwłaszcza do obróbki o wysokiej precyzji.
Układ serwo obrabiarek CNC jest jednym z kluczowych systemów ruchu osi maszyny, obejmującym ruch posuwowy, ruch wrzeciona i sterowanie położeniem. Jego działanie ma istotny wpływ na dokładność powtarzalnego pozycjonowania, charakterystykę odpowiedzi dynamicznej obrabiarki CNC i maksymalną prędkość ruchu w swobodnym zakresie. Jednocześnie rozwój serwosystemów miał nieoceniony wpływ na rozwój obrabiarek CNC.
Segmentacja rynku | Producent głównego nurtu | |
Rynek z niższej półki | Podwójny uchwyt na elektronarzędzia | SCHOTT, Dipma, Yantai Global, Shenyang Machine Tool |
Rynek średniej i wyższej półki | Podwójny uchwyt na elektronarzędzia | SCHOTT, Dipma, Balafati |
Rynek z najwyższej półki | Pojedynczy uchwyt na elektronarzędzia | SCHOTT, Dipma, Niemcy EWS, Niemcy LARU |